API 687: Chapter 0, Section 10 - Inspections (ITPs, PMI and Hardness)
- Fernando E. Romero, P.E.
- Aug 4, 2024
- 10 min read
Updated: Aug 10, 2024
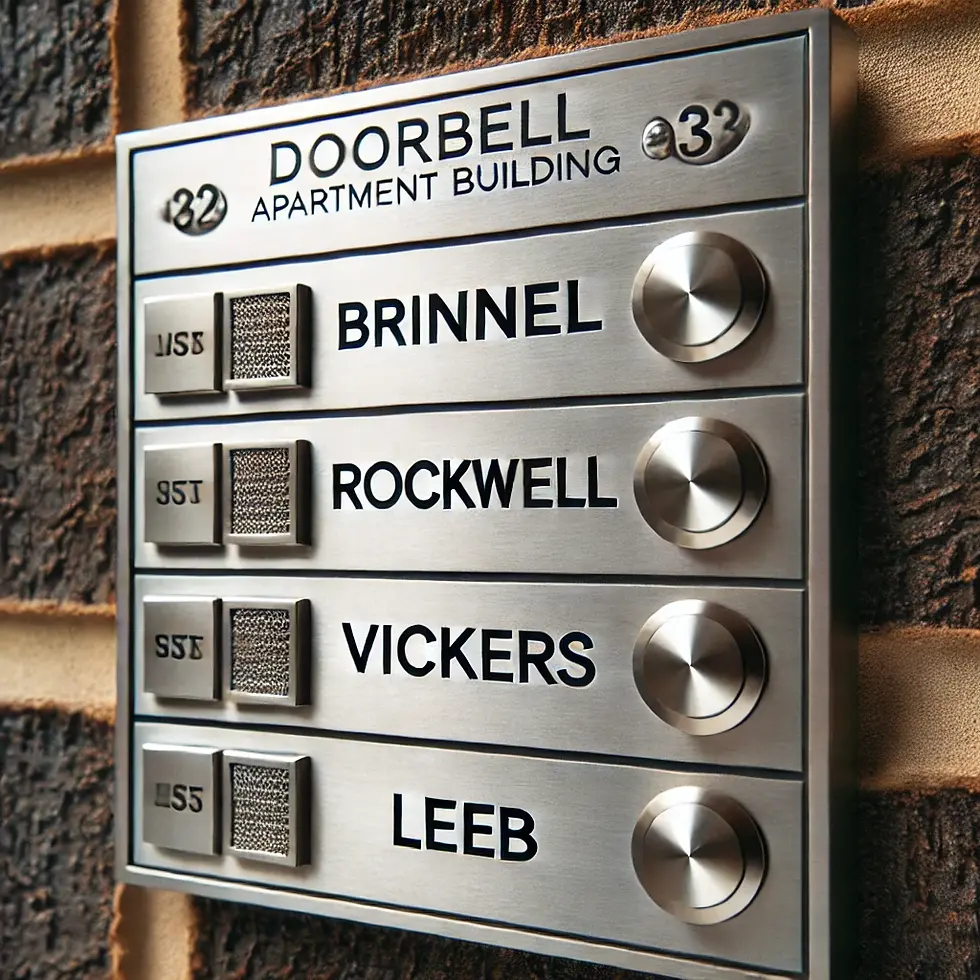
The first statement in Section 10 is a “Statement of Purpose”, and I have a bit of trouble with it because it contains the word “should”. Statements of purpose are meant to be a definitive and clear declaration of intent and do not contain words like “should”.
This is what RP 687 says: “The purpose of an inspection SHOULD be to allow an accurate representation of the condition of…”
I can’t accept this. This statement is not a recommendation or a guideline. It is a statement of purpose. So, I am going to be a purist and insist and set the record straight.
The purpose of an inspection IS to allow an accurate representation of the condition of the assembly or component.
To make you believe me, I had my version of the statement translated into Yoda speak:
“To allow an accurate representation of the condition of the assembly or component, the purpose of an inspection is.”
Ok, I am glad we are over that. I struggled for two weeks on how to get over that one sentence.
The Importance of Cleaning and Inspections
Section 10 offers general guidelines mainly on cleaning and preparing parts for inspections.
One point on which the document insists is that the equipment owner clearly communicates and sets requirements for witnessing inspections.
Remember, taking a machine apart and inspecting it is the same as having a team of forensic engineers study a crime scene.
Both will be applying engineering principles and scientific methods to investigate and analyze physical evidence related to an incident.
The process of taking things apart and inspecting them can be a disruptive process, meaning it affects the condition of the crime scene.
Often, some inspections can only be done properly once.
For instance, if a coupling is removed but its condition was not properly documented prior to removing it, there is no way to put it back with certainty that it will represent the actual condition it had.
Removal processes often require the application of heat and force that alter the condition of an assembly or a part, and that “effect” cannot be undone.
So, measure twice and remove once.
A great tool that ties the concept of performing inspections and quality control is called an Inspection and Test Plan or ITP.
ITPs are mentioned three times in API RP 687. As a matter of fact, all the mentions occur in Chapter 0: once in Section 15, when the document suggests guidelines for what should be included in a proposal for inspections; and twice in Annex J where the document suggests the overall planning requirements of an outage.
The next time the RP 687 document is revised we must suggest that there is more emphasis placed on the importance and usefulness of ITPs. Since most inspection instances and methods are known and prescribed by API RP 687, we could even provide a general template.
I put this much emphasis on ITPs for two reasons:
One, if the test plan is written, it can be easily communicated within all parties. This means all parties can review and agree and avoid any surprises.
Secondly, within the ITP, an owner can specify hold and witness points. And once again, since this is a document, it can then be communicated and mutually agreed and observed.
Many times, in my career I have met customers that were dissatisfied with the fact that they missed an inspection or did not get to see something they wanted to see done to their equipment.
Owners must remember that once a shop is cut loose and the work is released, mechanics want to take everything down to its last nut and bolt.
So, it is extremely important to make wishes of hold points and witness points known.
Shops must remember that the owner’s equipment engineers may have been waiting years for an overhaul to occur so they could finally be present when the equipment is taken apart to see things for themselves. There is nothing sadder to an engineer than having missed an opportunity to see a machine taken apart.
So, hopefully, on the third edition of API RP 687 there will be more emphasis on the use of ITPs.
The document continues with a set of recommendations for two subcomponents that are important and deserving of some discussion.
Coupling and Dry Gas Seals.
Both of these components should be removed and inspected by a qualified vendor.
Couplings are both beautiful and underrated components in rotating equipment. They are often removed in the field, shared across multiple rotors, and are highly stressed components that provide a unique function.
We could spend days discussing coupling designs or exploring API STD 671 “Special Purpose Couplings for Petroleum, Chemical and Gas Industry Services”, but the main reason couplings are mentioned here is because of the tapered hydraulic coupling.

These couplings are usually found in compressors, and what you must know is that all the power and torque transmission that goes from the driver (motor, steam turbine) into the shaft of the compressor and into the fluid is transferred by the “contact pressure” or “interference” between the coupling and the shaft.
Like a tight handshake and nothing else, no keys, no fasteners, nothing, just sheer pressure.
If you want to level up into the ranks of ultra nerd, then search for a copy of Engineering Considerations of Stress, Strain and Strength by Robert C Juvinall (Professor of Mechanical Engineering, University of Michigan). (ISBN 0070331804)
In this book, Juvinall cleverly quips you with all the equations you need to calculate the stresses on radially loaded cylindrical members, including concentric cylinders with interference fits.
Concentric cylinders with interference fits are basically the scientific name for “Couplings”!!!
It’s ok if you’re not as excited as I am. For me, couplings and understanding how they work were one of my first assignments as an engineer. I’ve studied them, characterized them, written calculators on them, performed FEAs on them, and I even made some bookends out of one once!
There are a few challenges and reasons why RP 687 suggests having a qualified vendor handle a coupling inspection.
Coupling bores are critical due to the multiple functions they provide. The inner surface of the bore must be perfect so the contact to the shaft is also perfect.
Inspecting the bore of the coupling is extremely difficult without a “standard”, “plug gauge” or some specialized metrology tool.
A standard or plug gauge will only provide a picture of the quality of the surface of the bore, but not its condition of alignment.
The alignment of the bore must be perfect on the axis of rotation.
These are some of the reasons why coupling inspections and balancing are often relinquished to qualified coupling suppliers.
The next component API recommends is assessed by the experts that made them: mechanical seals, particularly dry gas seals. These seals are complex assemblies made by a handful of seal manufacturers and are filled with proprietary design details and features that require the expertise of the manufacturer.
That is why it is best to remove the mechanical seal, sometimes under the watchful eye of the manufacturer, so they can briskly take the seal to their own lair to be disassembled, repaired, and tested in accordance to API 692: Compressor Dry Gas Seals before being returned to the main shop.
Statement 10.1.12 asks to determine the chemistry and hardness of components
One simple statement and a lot to talk about.
When you are dealing with metals, you must always know two things about the metal:
what is the chemical composition of the metal
how strong is the metal
For instance, not all steels made of the exact same chemical composition have the same strength, the strength and other mechanical properties of a material are determined by the heat treatment they received during manufacturing.
Heat treatments allow us to make metals that can be soft and ductile or hard and brittle.
Positive Material Identification or PMI
Positive Material Identification or PMI is the process of identifying a metal’s chemical composition and there are three main methods used:
Portable XRF Analyzers These look like a blackberry had a baby with a hair dryer. They shoot an X-Ray beam that knocks out some of the electrons in the elements of the metals. Each element has a unique energy signature when this happens that is measurable by the device. The only limitation of XRF analyzers is they have a hard time detecting the Carbon content, so it is not suitable for some alloys. This method is useful because it is portable, and it can be carried around the shop.
Optical Emission Spectroscopy (OES) These are larger machines usually found in test labs. They use an electric arc to once again excite atoms in the metal. The equipment then measures the emitted light and detects which elements are present in the alloy including Carbon. This method is accurate, but the draw back is the parts need to be taken to the equipment. There are mobile OES units that can be wheeled out to a shop, but for some reason most facilities rely on handheld XRF units or the next method.
Metal shavings + OES The last method employed consists of removing “metal shavings”, usually by taking a drill bit and removing a tiny bit of metal from a shaft or another non-important place on a rotor or component. All is needed is a handful of shavings that later get pressed into a tiny disk that is then fed into an OES machine. So, the third method is really OES, but instead of taking the machine to the part, one takes metal shavings to the machine.
If you are an equipment owner and are expecting to have your repair partner PMI your parts, make sure you specify OES as the method. In turn, the repair shop should then ask you for permission or advice as they will be taking metal shaving samples of a non-relevant area of your parts.
The next task of determining the mechanical properties of the metal is much more difficult.
Out of all the mechanical properties, the following are the most useful when evaluating the condition or design of a part:
Tensile Strength There are two characteristics of tensile strength: These two properties are measured in terms of stress or pounds per square inch.
Ultimate Tensile Strength or UTS: the maximum stress that a material can withstand while being pulled or stretched before breaking.
Yield Strength: the stress at which a material begins to deform plastically. A material stressed below its yield strength will deform elastically, meaning it returns to its original shape when the stress is removed.
Ductility Once again, there are two characteristics of ductility: These two properties are measured and expressed as a percentage. Elongation of a percent of the original length and reduction of area as a percentage of the original area.
Elongation: the ability of a material to deform before it breaks when being pulled.
Reduction of Area: as a part deforms when pulled or stretched, its cross-sectional area will become smaller. Once the part breaks, the reduction in area is measured.
These two sets of parameters are measured during a test called the tensile test, which is standardized and governed by the ASTM E8 Standard Test Methods for Tension Testing of Metallic Materials standard.
This requires cutting out a small cylinder of material from the sample, so this method is considered destructive and cannot be used if a part is to be re-used.
This method is always used when qualifying raw material or working with a scrap part.
Hardness
Since destroying good parts is not always possible, an alternate method for determining a material’s condition is by measuring its “hardness”.
Like I said before, all material properties can be altered or set by applying heat treatments.
We’ve all seen the movies where the blacksmith takes a sword that is red hot and after pounding on it with a hammer, he dunks it into a bucket.
This is actually a heat treatment, and it is called quenching.
You would not want to cut a good-looking sword in half to measure its properties, so instead you measure its hardness.
You correlate the hardness of certain metals to their heat-treated condition and, therefore, to their tensile strength.
The best method to test hardness is to bite into the metal and see the size of the toothmarks left behind.
Now I am being silly, but scientifically, that is what the methods used to test hardness do.
They all use some device to leave an indentation and to measure and correlate the size of the indentation to a value of hardness.
The measures and scales used are highly dependent on the method, so much so that the methods and their units of measure have the same name.
There is the Brinell method, the Rockwell method, and the Vickers method, to name the most popular and reliable. Rockwell and Vickers use a tiny diamond as a tooth to press and indent into the measured material with a known force, Brinell uses a spherical indenter to do the same. When the force is removed, the size of the diamond indentation will tell us the hardness of the material.
Like in determining chemical composition, it seems that the portable methods used for measuring hardness have limitations on accuracy, and the better methods require taking the measured parts to a laboratory.
The two most deployed portable methods for measuring hardness are known as:
UCI for Ultrasonic Contact Impedance: This method uses the Vickers measurement and works by using ultrasonic vibrations. The ultrasonic vibration impedance on the test probe will be affected as the Vickers diamond tip presses into the metal. I know this is a lot to take in and I am oversimplifying it a bit.
The next widely spread portable method is called the Leeb rebound hardness tester. This method basically drops a tiny tungsten ball onto a metal, and it measures how much energy is being absorbed or lost as it bounces.
If you want to learn more about these and other hardness methods, there is an incredible eBook which you can download after registering at this particular Swiss manufacturer’s site: SCREENING EAGLE / proceq
I am personally not very fond of portable hardness measurements. Their reliability is greatly dependent on the skill and competency of the technician, the condition of the equipment, and the process used.
Essentially, you need a trained specialist willing to follow the discipline of checking his skills against a calibrated standard every time they are going to make a work measurement. Afterall, hardness measurements will be used to infer other mechanical properties, therefore reliability and accuracy are of the utmost importance.
Commenti